"Working principle and application of roller mill"
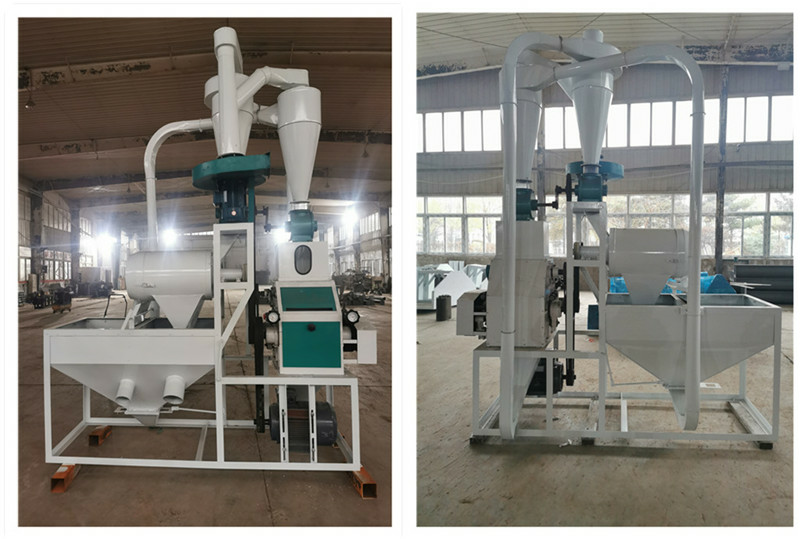
Roll mill is a commonly used equipment for material processing, mainly suitable for medium and fine crushing of medium hard and soft ores. This equipment mainly consists of rollers, roller support bearings, compression and adjustment devices, and driving devices.
The discharge particle size of the roller mill can be adjusted by wedges or washers installed between the two rollers of the equipment, thereby achieving precise control of the particle size of the finished material. The driving mechanism is composed of two electric motors, which are transmitted to the groove wheel or shaft through a V-belt or reducer, and the roller is dragged to rotate in relative directions.
In addition, the vulnerable parts of the roller mill are very wear-resistant and durable. If hard materials are crushed, these vulnerable parts can be used for more than a year. If the crushed materials are soft, they do not need to be replaced after three years of use, which greatly reduces production costs.
It is worth mentioning that if irregular rollers are used, that is, the two rollers operate at non equal circles, non meshing, and non equal speeds, it can further reduce material blockage and improve the stability and efficiency of the equipment.
The roller mill is a type of powder making equipment that combines ring roller grinding with air flow screening and pneumatic conveying. It has the characteristics of strong universality, continuous dry powder making, concentrated particle size distribution, continuously adjustable fineness, and compact structure. The particle size of the finished product can be adjusted within the range of 80~425 mesh, and even 30~80 mesh coarse powder can be produced by adding special devices.
The working principle of the roller mill is mainly divided into two steps:1. The material first enters the center of the grinding wheel through the feeding hopper, and is then ground into fine powder by the grinding wheel. During this process, grinding wheels are usually made of high hardness wear-resistant materials to ensure long-term use without wear. The powder is further finely ground through the gaps between the grinding wheels.
2. The ground powder is transported by the airflow of the fan and enters the analyzer for classification and screening. The finished powder that meets the product particle size requirements will enter the collection device for output under the airflow transportation, while the powder that does not meet the requirements will be returned to the main grinding room for secondary grinding.
The application of roller mill is very extensive, which can be used in metallurgy, chemical industry, mineral processing, building materials, food, medicine and other fields. For example, in the metallurgical industry, it can be used to grind various ores to extract valuable metal elements; In the chemical and pharmaceutical industries, it can be used to prepare various chemical raw materials and drugs; In the food industry, it can be used to grind various ingredients to make various nutritional powders and additives.